Technologies
Over the years, PlaneWave has introduced product features such as on-axis encoders, direct drive motors, and turn-key off-the-shelf large aperture observatory systems, all of which are now industry standards in the global astronomy market.Â
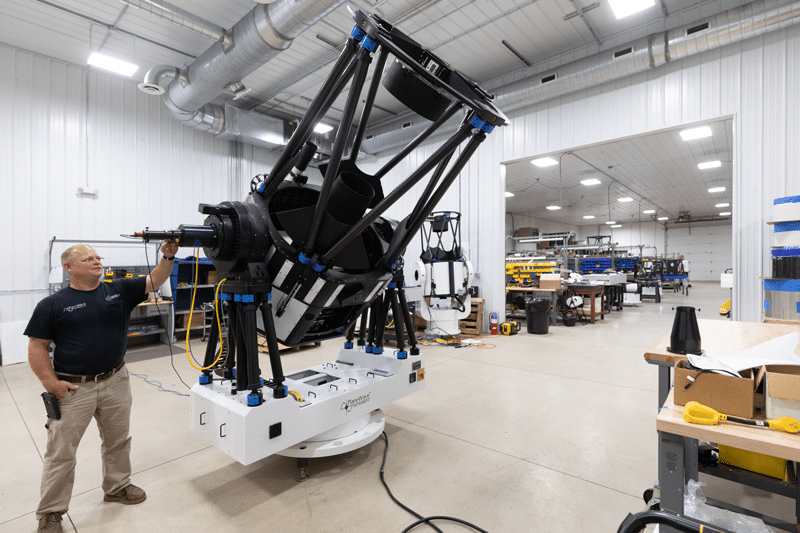
CDK Optical Design
CDK is the original optical design created by our founders to make an affordable astrographic telescope with a large enough imaging plane to take advantage of large format CCD cameras. The old RC telescope design was hard to make and expensive, while the new CDK design performs better and is much less expensive to create.Â
The CDK consists of three components: an ellipsoidal primary mirror, a spherical secondary mirror and a lens group. All these components are optimized to work together to create superb pinpoint stars across the entire 52 to 100 mm image plane. To prevent degraded images, the CDK is coma free, has no off-axis astigmatism, and has a flat field.
Production
The next innovation was to manufacture telescopes using repetitive manufacturing practices, creating dedicated telescope lines to produce the same items all year round. At the time, almost all telescopes were custom-built, which made them very expensive to purchase and even harder to maintain and repair.
At PlaneWave Instruments, each optical component of our systems goes through an extensive process of figuring, testing, and inspection to guarantee excellent performance from every telescope we produce. Every one of our telescopes is tested as a complete, finished system in one of our modern test bays to ensure that each optical system is of the highest quality before it is shipped to a customer. Because our test bays are independently temperature controlled, we can reduce atmospheric fluctuations that typically affect on-sky measurements, allowing for the most precise measurement of the quality of the telescope. This allows our expert technicians to efficiently identify and correct any residual alignment or figure errors in the complete optical system.
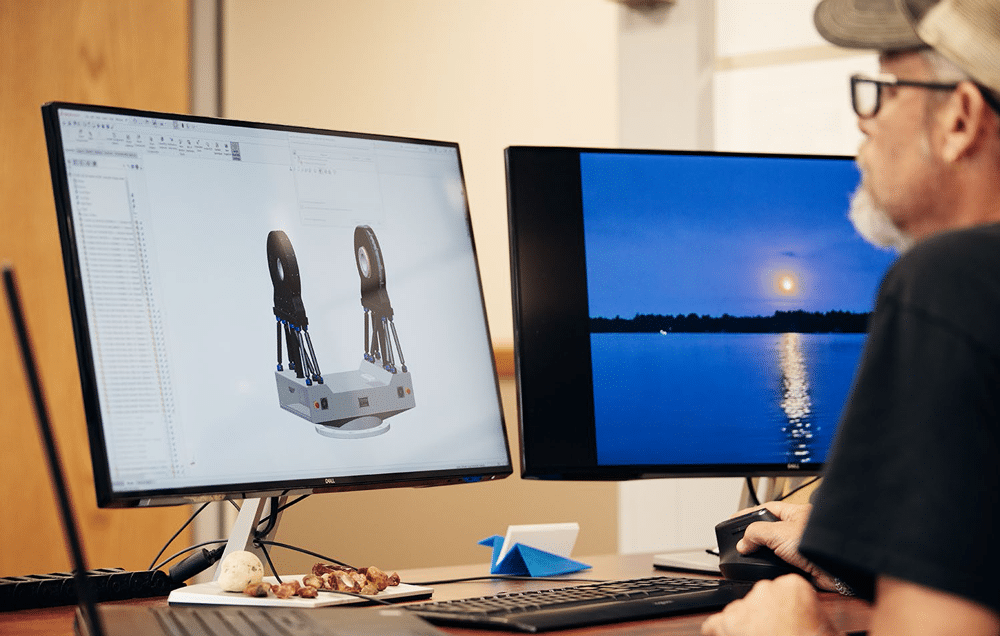
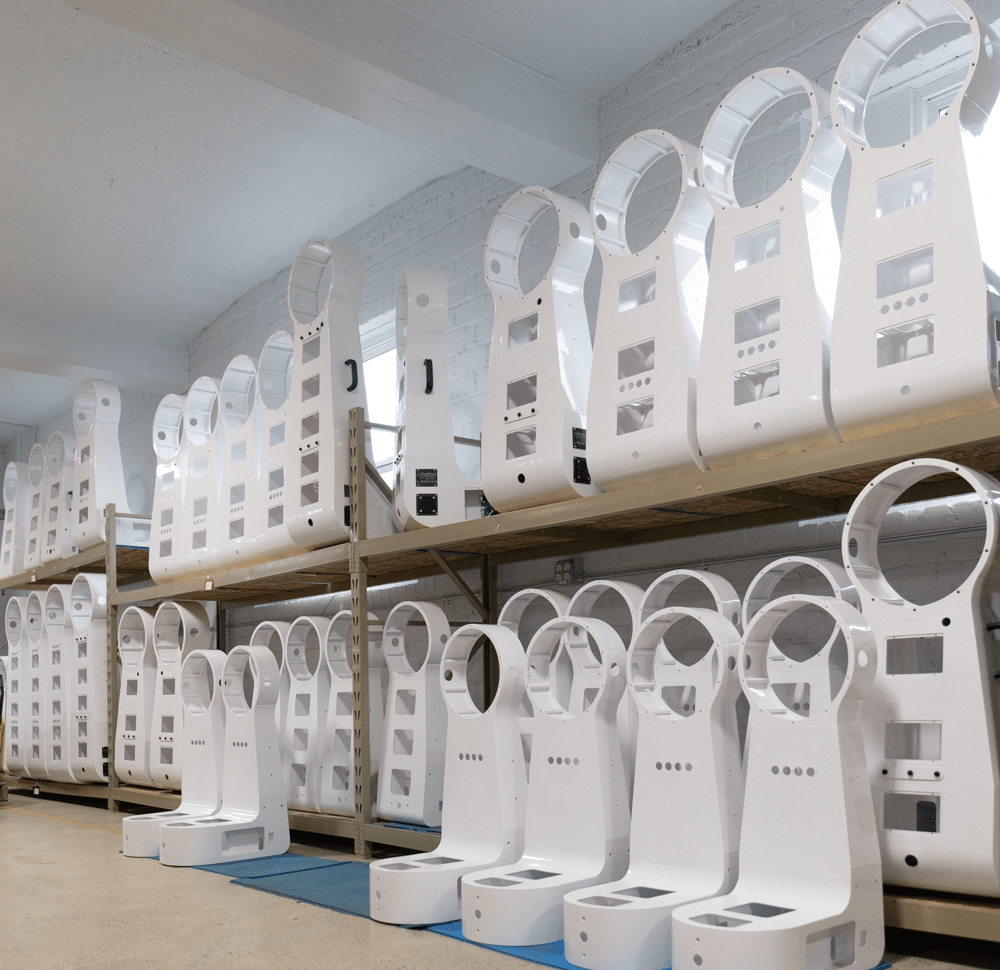
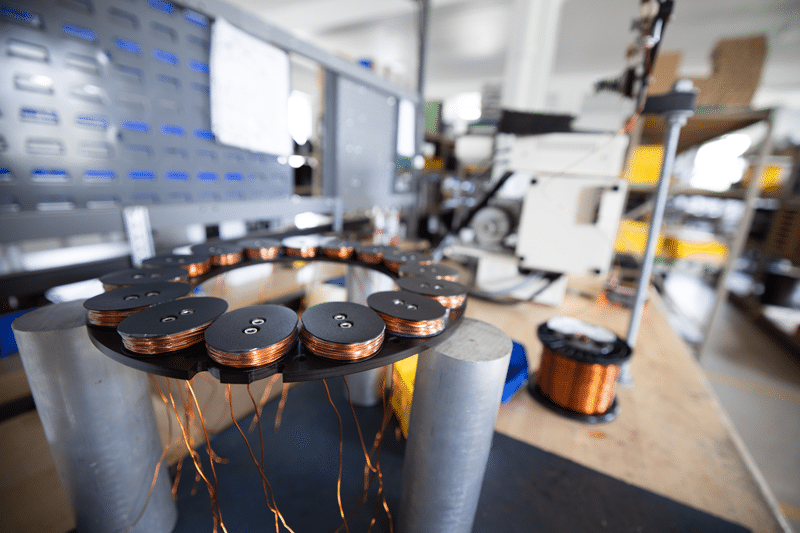
Direct Drive Mount
Direct drive motors were extremely expensive but solve some of the stability problems caused by gear mounts. Direct-drive motors contain no gears to cause backlash or periodic errors while slewing and tracking, allowing the telescope to move at incredible speeds for tracking satellites or to minimize target acquisition time.
By bringing down the cost of direct drive motors, we made them more accessible while producing significantly better imaging. We manufacture our own direct-drive motors to provide high precision tracking and pointing accuracy for demanding client applications all over the world. All direct-drive mounts come standard with high-resolution 26-bit encoders on both axes to provide feedback during tracking and slewing.
Optics and Glass Machining
Our telescopes have had lightweight glass since almost the beginning, but we made this a more efficient part of our manufacturing process by creating the mirrors on-site. Our technicians use a custom optical metrology measurement system to generate a precision surface wavefront map for every mirror at each stage of the manufacturing process. This data is used in one of our state-of-the-art, robotic optics figuring machines to smooth and correct any errors present in the mirror surface. This measurement and figuring process is repeated until each mirror meets the exacting quality required for every PlaneWave telescope.
After final figuring, our mirrors are coated, inspected, mounted in their support cells and the optical quality measurement is repeated to ensure that no surface errors have been introduced during the process. This is a critical step to ensure that the mirror will perform when installed into the completed telescope. Many other manufacturers skip this important test to remove astigmatism and other errors from their measurements. These errors cannot be ignored since they are detrimental to the quality of the complete telescope. No mirror passes on to final assembly without verifying the complete surface wavefront.
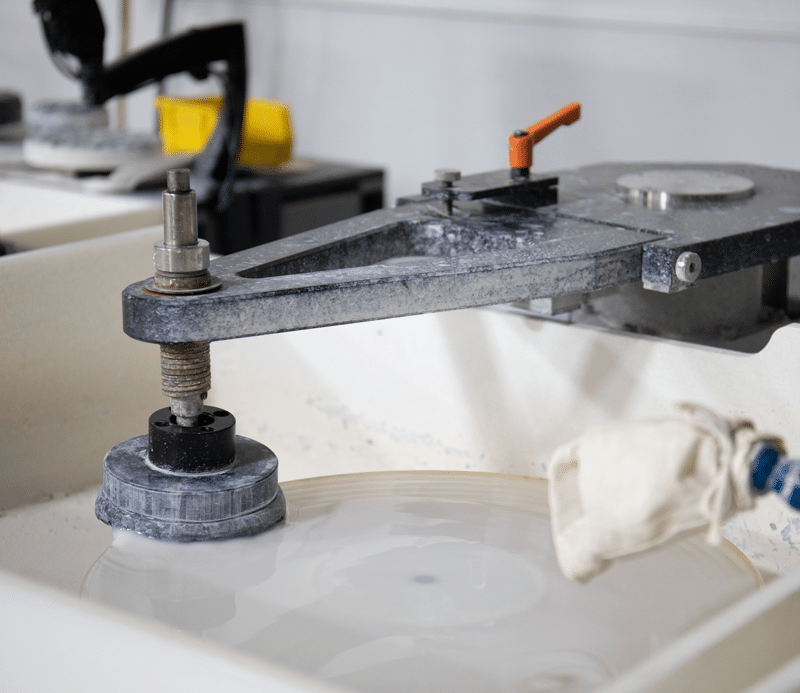
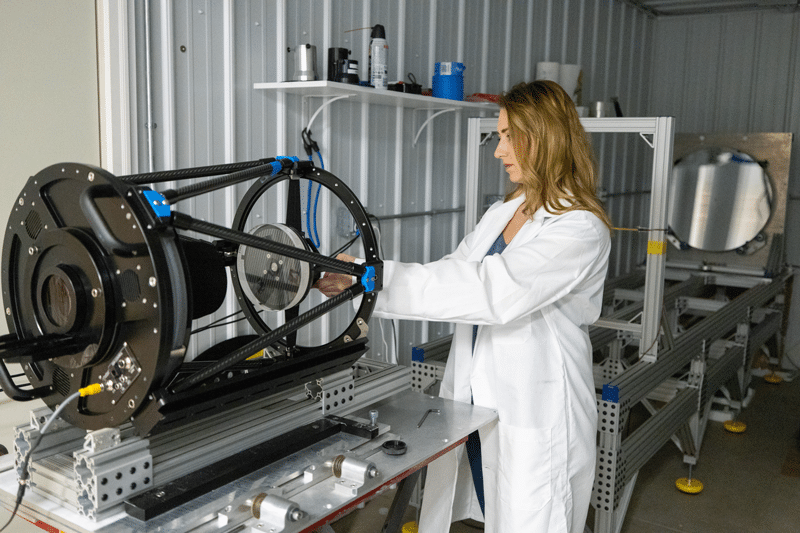